When first considering the Jersey Business’ Business Improvement Programme, Pascal Maurice, Managing Director of Granite Le Pelley, was curious. In the 12 years that he has worked at Granite Le Pelley, the business has gone from strength to strength, as the largest stone company in the Channel Islands. He certainly wasn’t expecting the programme to kickstart a chain reaction which would ultimately set the business on a path to digital transformation.
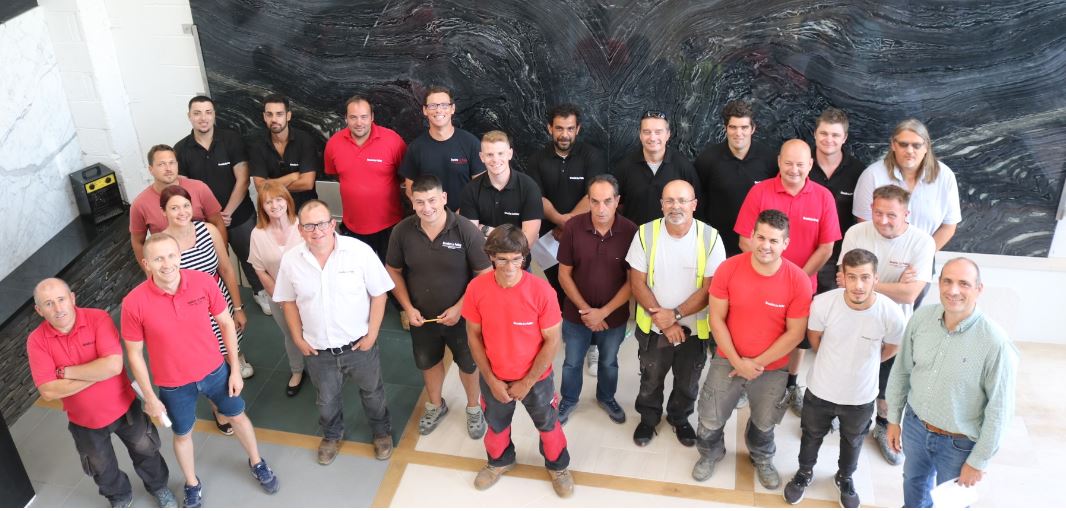
“Businesses need momentum. We knew that to keep growing, we needed to change but we weren’t sure what should change or where to start. We took part in the Business Improvement Programme at exactly the right time.”
Adapting to new challenges
Granite Le Pelley had recently taken on a new project, larger and more complex than much of their more typical work. The sudden change in volume of work, in particular the need to produce substantially more paperwork, presented some challenges.
“For a typical project we will produce around 50 drawings, but in this case, we created more than 1,000. We would normally print the drawings, laminate them, and deliver them to the stone mason. If they get lost or need updating, we deliver the new drawing. That worked well up until now, but it wasn’t a scalable solution.”
Embracing digital transformation
It is fair to say that the construction industry has been slower to adopt digital solutions compared with other sectors. According to research from McKinsey in 2016, the industry was among the lowest digitised, contending only with agriculture for the bottom spot. However, in the six years since, opportunities have been realised and many construction businesses are questioning how they can use technology to improve their organisations.
For Granite Le Pelley, the Business Improvement Programme gave them time and space to focus on the issues they were encountering, while opening their eyes to the potential solutions. Rather than manually printing, laminating and delivering drawings for their new project, the business has invested in tablets which can receive the drawings and any subsequent changes.
“The programme really helped us to zero in, giving us a starting point. Suddenly we could see that by making a few changes at the design stage and investing in technology and training, we could become much more efficient. We estimate that this has already saved us £3,000, and we have been able to apply this thinking to other areas of the business.”
Following the programme, Granite Le Pelley began working with an external developer to help them digitise more processes. Two employees undertook the Business Improvement Programme, leading to improved data collection, sharing, and analysing. This saves the business around four hours a week and has led to a deeper understanding of projects and processes.
“We have invested approximately £30,000 in digitisation so far, but we are already seeing a return in terms of improved efficiency. As well as saving time and money in the long run, we are also able to better adapt to external factors by, for example, working from home. The transformation has made us more agile, competitive and innovative, and we are still very much at the beginning of our journey.”
Lean six sigma
As a result of Granite Le Pelley attending the Business Improvement Programme and subsequently completing their project, the individuals have been awarded the Lean Six Sigma Green Belt certification. Lean Six Sigma is based upon the Six Sigma methodology for business improvement and companies known to use this in some form include Amazon, Boeing and General Electric.
“I’m extremely proud of the work we have achieved since beginning our digital transformation process and am grateful to Jersey Business for giving us the jump start, and the skills we needed to navigate this successfully.”
Pascal Maurice,
Managing Director of Granite Le Pelley,