Waste: whether it’s a waste of time, a waste of resources, or a waste of money, it's a word that conjures images of inefficiency and lost potential. At its core, waste encompasses any activity that consumes time without directly adding value to the customer. Think of the countless hours spent searching for information, tools, or documents buried in the digital abyss.
Studies suggest that up to 50% of the world's economy is tangled up in wasteful activities. Looking closer to home, it’s been reported that employees in the UK spend 360 hours a year searching for information within their business that should be available almost instantly. This comes at a cost of nearly £10,000 per employee for organisations. It's a sobering statistic that demands attention, especially as we strive for a more sustainable, productive, and efficient future.
But how can we tackle waste head on to ensure it doesn’t limit any business’s potential?
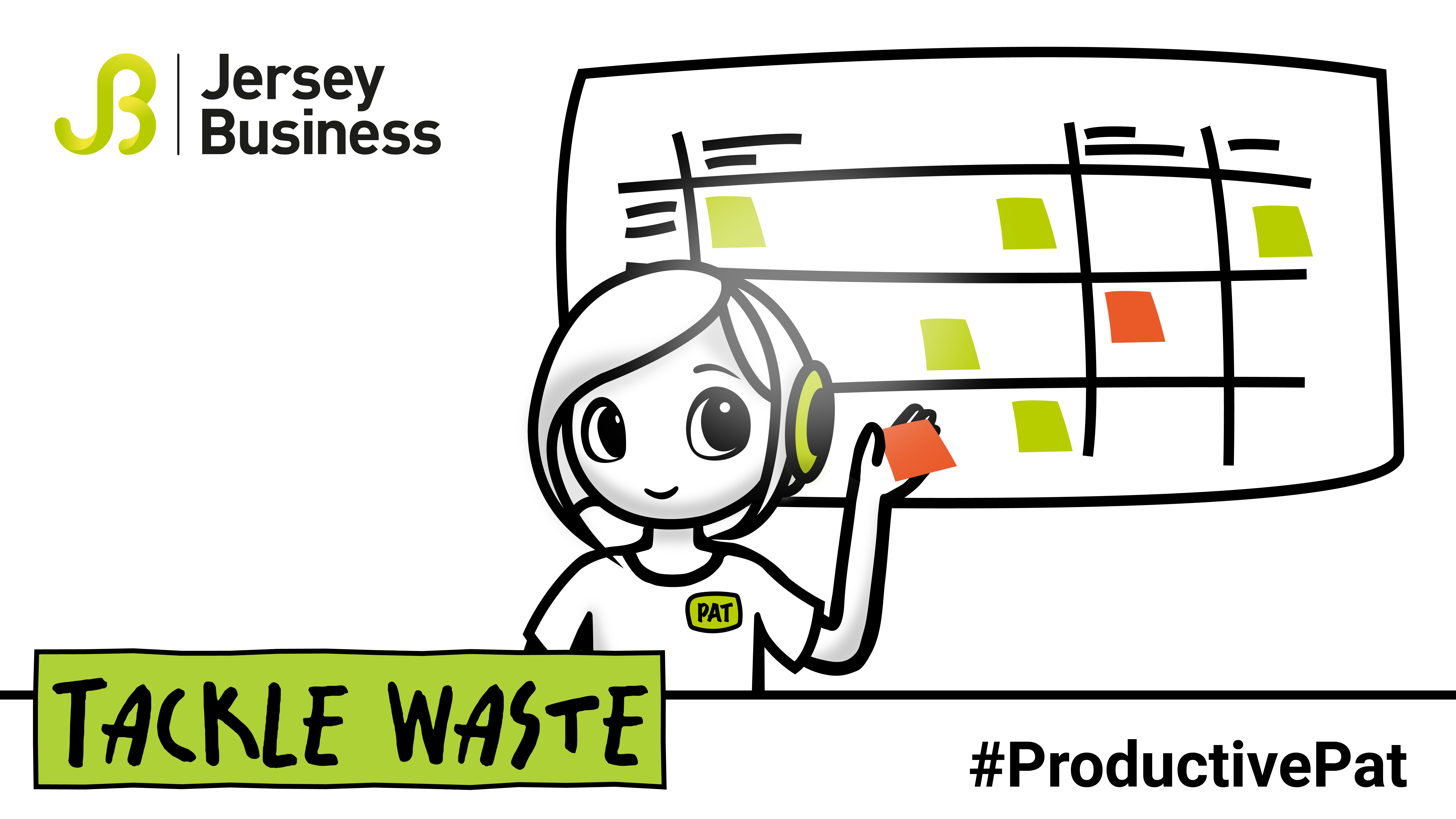
Understand the Seven Wastes (MUDA)
Created by Taiichi Ohno, the seven wastes - or MUDA - refer to different categories of problems organisations may run into that cause levels of waste.
- Defects: As the name suggests, it’s anything that is supplied to you or a customer that is wrong. This could be an incorrect brief, unfinished files, or broken products. Simply, anything defective will likely have to be done again and could lead to customer dissatisfaction.
- Over production: Making too much of one product, following a just in case mindset, can lead to over production and wastage. This is especially true in sectors where goods and products have a certain shelf life.
- Waiting: Ever got a job done efficiently but then waited days, if not weeks, to receive feedback and keep going? The time lost waiting can equate to hours of waste.
- Inventory: Excess inventory tends to hide problems and inefficiency within a business. It increases lead times, consumes productive floor space, delays the identification of problems, and inhibits communication.
- Transportation: While this was initially used for the literal transportation of goods, it can be relevant for all business types. Think about the movement of paperwork, multiple hand-offs of electronic data, approvals, excessive email attachments, and distributing many copies to people who may not really need them. These take up valuable time and resources.
- Unnecessary processing: You wouldn’t use a sledgehammer to crack a nut, so why buy expensive, high precision equipment where simpler tools would be sufficient?
- Excess motion: This waste is related to ergonomics and is seen in all instances of bending, stretching, walking, lifting, and reaching. These are also health and safety issues. Jobs with excessive motion need to be analysed and redesigned for improvement.
By knowing these seven wastes and being able to identify them in your own business, you’re less likely to have multiple inefficiencies that not only hinder productivity but also strain our resources and damage the environment.
Uncover Hidden Costs
Even with knowledge of the seven wastes, it’s easy to allow them to become the norm in your business’s processes. The best way to see the effects of these wastes, and do something about them, is to put a value to the resources lost.
Consider this scenario: an intellectual property firm realises that its team spends a significant chunk of time hunting for information that should be readily available. By assigning a monetary value to this wasted time, they uncover an eye-opening £176,000 drain on their resources annually. Imagine the financial impact of redirecting even a portion of that time towards more productive endeavours.
The key to addressing waste lies in measurement. By quantifying the time and resources lost to wasteful activities, we gain valuable insights into where improvements can be made. Remember, what gets measured gets managed – and ultimately, improved. If you accept poor performance, you’ll get poor performance.
A Practical Approach to Waste Reduction
So, how can businesses begin their journey towards waste reduction? Start by making processes visible and tangible. No need for complex flowcharts – a simple whiteboard session can reveal hidden inefficiencies and spark meaningful discussions.
Once you’ve gone through all the processes in your business, embrace a color-coded approach to waste identification. Red stickers flag areas of waste, prompting further investigation and action. Remember, simplicity is key – focus on recognising waste before delving into the finer details.
From Waste to Productivity
As you embark on this journey to cut waste and boost productivity, let's keep one thing in mind: your capacity for improvement is limitless. By empowering your teams to identify and address waste, you can pave the way for a more efficient and sustainable future.
Ready to tackle waste head-on? Start by mapping out your processes, identifying areas of inefficiency, and committing to continuous improvement. Together, we can turn waste into opportunity and unlock the full potential of our businesses.