As a business leader, you might feel that you know your processes back to front and inside out.
That may be true, but would everyone within your business make the same claim? Would they all agree on the ‘right’ way to do things for maximum efficiency, quality and productivity?
Think for a moment about making a cup of tea. Every point from deciding you’re thirsty to draining the last drop is a step in a process.
Perhaps you put the kettle on first and then collect your mug, or maybe you do that the other way around. You might check your emails while the kettle boils and pop back when it’s done. You could be a milk-first type or opt for no milk at all.
The point is that there are several variations throughout the process. We all think that we know what it means to make a cup of tea, but the steps we take to get to that end result might be vastly different.
This is the same with your business processes.
Only by understanding, analysing and standardising your processes can you ensure maximum productivity and minimal waste. So, here are the steps to get started on defining a process for your business.
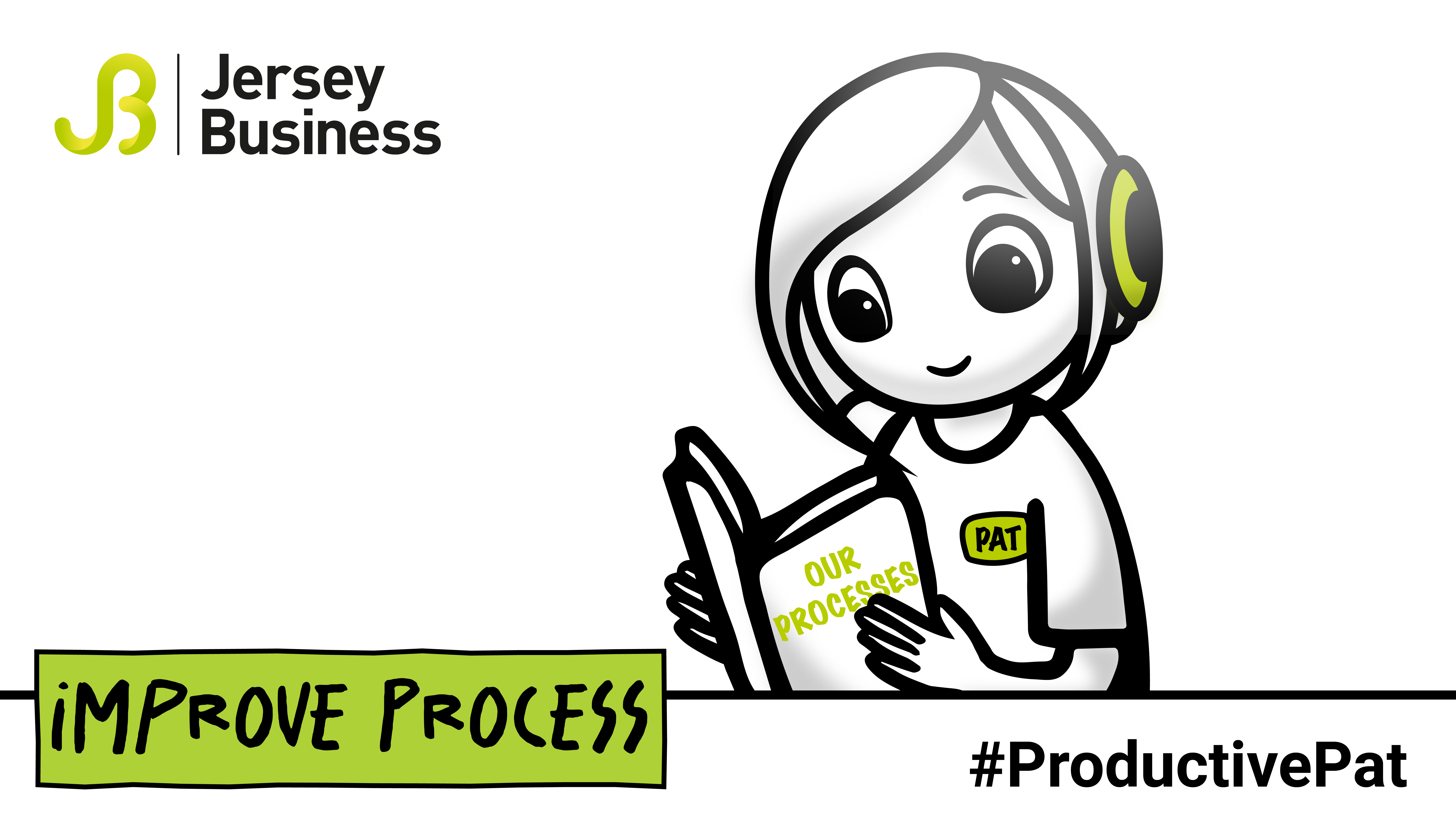
1. Determine each step in the process
A simple exercise we recommend for businesses to undertake is to first determine each step in a process.
Take the time to think about what should happen when and by whom. Do this before getting the involvement of your employees, so that you move into the next stage with an idea of how things should go.
2. Monitor what is really happening
Often we find that there is a gap between the planned process and what actually happens.
There can be lots of reasons for that, from the ideal not working in practice, to a lack of communication when it comes to sharing the process. Either way, it’s important to determine both what you think should be happening and what is actually happening.
3. Focus on the big-ticket items
It can be easy to get bogged down in the details in an exercise like this but focus on the key parts to stop things from becoming too complex.
You’ll likely find that there are one or two areas where a lot of waste is occurring so these will naturally become your first to tackle.
4. Standardise it
A process is only efficient if everyone is following it in the same way.
Once you’ve worked with your employees to determine the best process, it’s vital to communicate this throughout the business and ensure it remains common practice.
5. Don’t forget your supply chain
There are external processes that will have a knock-on effect on your business. If there is something happening in your supply chain that is having a negative impact, don’t be afraid to start conversations about improving processes that can involve you both.
Keep it positive – there likely is a reason behind the way they operate – but don’t accept poor performance either.
Maximising the efficiency of your processes is a key way to ensure your customers receive the best quality product or service from your business whilst you increase overall productivity.
By refining and standardising your processes, you ensure your customers receive a quality experience every time whilst you as a business save valuable time and money by cutting out unnecessary waste.