A Business Improvement Programme success story
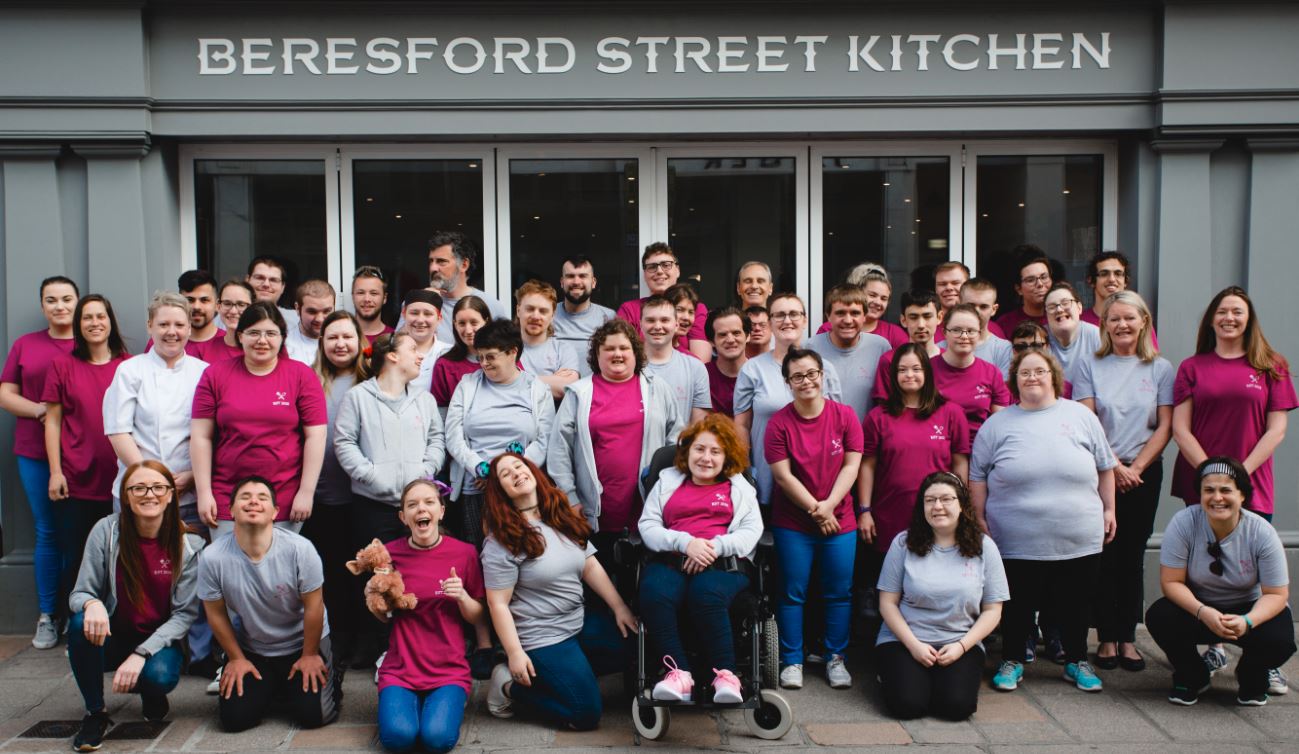
Beresford Street Kitchen (BSK) is a social enterprise providing education, training, and employment for people with learning disabilities and/or autism. BSK has four main areas: Beresford Street Kitchen, La Hogue Bie Tearooms, BSK Catering, and BSK Print Works.
BSK believes that people have the right to access learning and development at any age. The charity delivers learning and development through a holistic programme that focuses on education, workplace training, and employment progression where appropriate.
Taking part in the Business Improvement Programme
Ella Vieira and Bec Single took part in our Business Improvement Programme (BIP) with a focus on the Print Works division. The Print Works provides a high value of income to BSK with vast public exposure however, the volume and complexity of orders were outgrowing current processes with constraints on equipment, materials, workspace, and staff.
The peaks and troughs of activity created delays to order completion with bottlenecks in processes, particularly around scheduling and order management, leading to waste and duplication. The team set early project objectives that they wanted to meet by taking part in BIP:
- Reduce waiting times and bottlenecks in processes.
- Reduce errors or lack of data on communications and enhance live data access.
- Expand the visibility of Print Works through marketing and branding.
- Improve scheduling to optimise multi-sized orders.
- Maximise space utilisation.
By having a clear understanding of the challenges they’d like to overcome through BIP, Ella and Bec were able to begin by highlighting key issues areas in the current flow of work. They did this by using the ‘seven wastes analysis framework’, which shines a spotlight on any current processes that take up significant resource or cause workflow issues.
Issues noted included order issues, waiting delays, unnecessary processes, stock and supply chain difficulties, equipment concerns, and data discrepancies.
Overall, these topics were boiled down to key areas of improvement needed. These included:
- Improved briefing processes.
- Improved communication to customers about the offering.
- More accurate data collection and deployment.
- Improved internal communication channels to support better organization and staff morale.
- Improved process for small and one-off jobs.
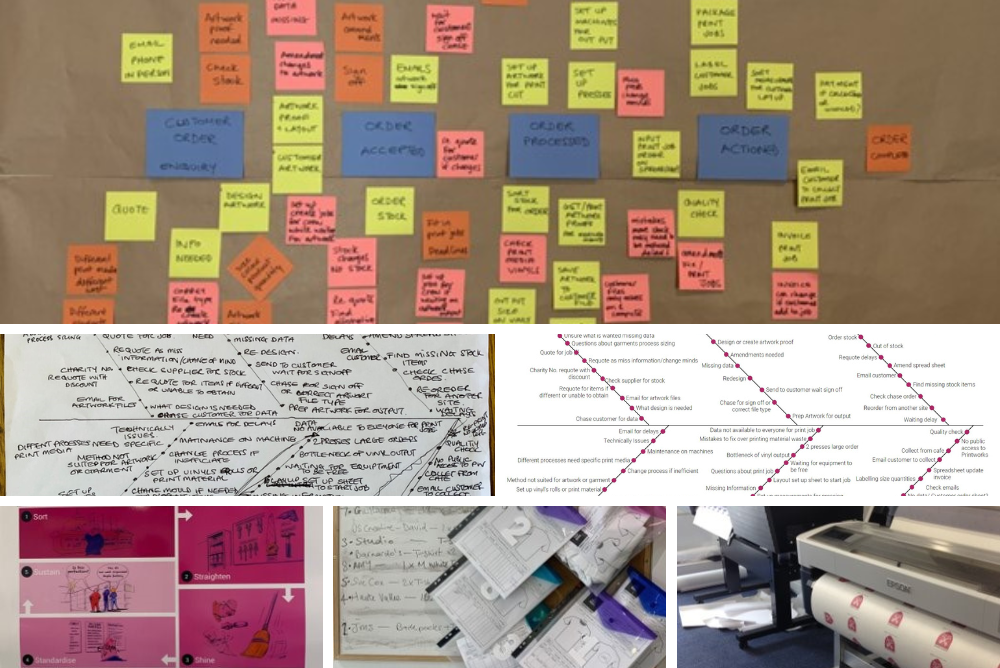
Using the learnings from BIP
Following BIP, the team are now measuring all these issues and finding solutions. This has led to:
- The creation of new processes with accurate and visual information accessible to all print staff.
- Machine efficiencies are now being optimised as the issues are addressed, providing a quicker turnaround of finished products.
- Sub projects have been set up to reduce rework and lost time across the whole printing process.
- Branding and communication of offerings are now enhanced to the public across the island as the business expands.
System changes have also been implemented to support a more efficient working process:
- Creation of an online print order system for existing and new BSK customers for quotes.
- Print Works order data is now made accessible to all staff enabling smooth flow of information for starting orders, reducing internal email communications and duplication within quotes.
- Efficient data recording within the manufacturing process which reduces errors and eliminates duplication.
- Introduction of new templates for customer communications on repeat and re-occurring orders.
Alongside these operational changes, the team have also reviewed their internal culture. No longer are they reacting to problems when they happen, they are proactively stopping them in their tracks.
The Print Works is evolving into a forward-thinking operational division of BSK. It’s using organisation-enhancing AI technology and is being proactive in managing costs and customer service. Continuous improvement is visible for all to see and be involved in, and the capacity for growth is an exciting passion held by all. After BIP, BSK was happy to share that, in the last three months, it has seen an increase in order throughput of 100% in volume and 90% in value.
Maintaining this level of improvement will see BSK double its income within the Prints Work from £50k to £100k per annum.
'Brian has a natural ability to turn what can be an overwhelming and daunting subject into an engaging and extremely enjoyable programme. His knowledge and support made implementing new and improved processes less intimidating and worthwhile. I would highly recommend the Business Improvement Programme to anyone....it will change your way of thinking forever!’
Ella Vieira, Programmes Manager & Safeguard Lead, Beresford Street Kitchen
‘One of the most interesting and insightful courses that I’ve ever taken. The BIP modules gave me a great understanding of how to apply productivity improvement in my workplace. Brian did a fantastic job of keeping us all engaged making things interesting with his personality and real-life stories, maintaining a good pace with great explanations on the subject matter. He was always available for questions during and in between modules. The BIP was very enjoyable for us at BSK, and we are now well prepared to apply what we have learnt to create a lean and efficient workplace’.
Bec Single, BSK Print Manager